With an increase production of wind towers required worldwide, and a universal problem of finding sufficient numbers of skilled and experienced welders, fabricators are turning more and more to automation to fill this gap.
It has always been the goal in offshore wind to find a welding process that can replicate the skills of a manual welder and provide a welding method that has the ability to follow an approved welding procedure, and plan the weld sequence just like a welder would do, as well as producing high quality welds. WeldLogic takes offshore wind industries a step closer to achieving this goal.
What is WeldLogic?
WeldLogic was created by Inrotech, and the system is based on years of accumulated welding experience and knowledge of semi-automatic and robotic welding. This information has been used to create a mathematical model of the welding processes and welding procedures which has then been incorporated into hardware and software to form the WeldLogic concept. It has been used in shipbuilding applications but are increasingly being deployed in offshore wind industries as the trend is going towards bigger structures.
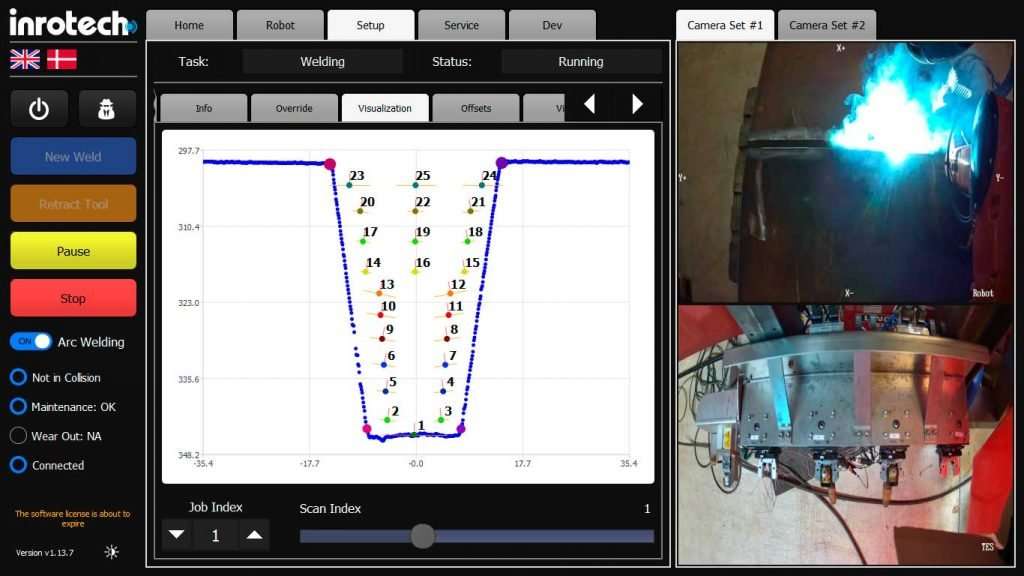
Automated welding robots with WeldLogic
Inrotech has developed various automated welding robot solutions based on WeldLogic technology. The Inrotech-C&B and Inrotech-Vertigo are specifically developed for offshore wind industries as they can be used to weld large wind structures. There is no need for CAD drawing transfers. No need of any kind of programming, teach-in routines, choosing of macros from pictures or scan or any other skilled or semi-skilled functions. During the welding process the robots automatically cuts the wire, cleans the welding torch and deslags the groove to ensure a perfect weld.
The system then applies the WeldLogic software which is able to cross reference data on the approved welding procedure for the joint being welded, and select the appropriate welding parameters to match the actual configuration.
When the scan is complete, full mapping of the weld preparation is available. From this information the software can calculate the weld volume required to complete the root, fill and cap passes for the given joint, providing a run sequence to match, just as a welder would do if welding this same joint manually. As the joint is being filled intermediate laser scans are carried out which allow for any necessary changes in weld deposition during the welding operation.
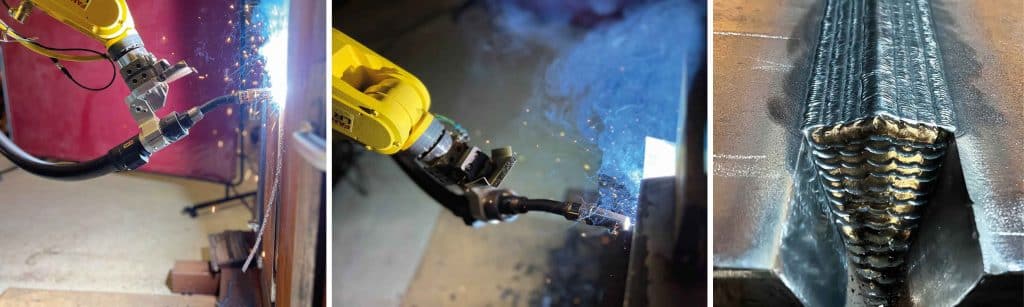
The operation – in summary
- The welding robot starts by performing a scan of the groove to be welded. This allows an analysis to be made of the weld groove, identifying its features and points of significance.
- The welding robot starts analysing the scans, finding the optimum selection of the welding parameters and distribution of the weld passes. This is done to ensure the groove is filled with an acceptable cap layer height and weld width.
- The WeldLogic generates a complete set of welding parameters for the whole weld, including welding speed, weaving amplitude, bead position, amps and volts etc, and with an inbuild inclination sensor this ensures the robot always knows the welding position and can thereby alter welding parameters to suit.
- The WeldLogic is also created by Inrotech and can store pre-approved welding procedures which are referenced for each welding application. Use of this database ensures that the welding being performed is compliant with the approved welding procedure specification (WPS) and ensures that the nominated welding parameters are strictly adhered to.
- While performing the weld, the WeldLogic system monitors and logs the actual welding parameters, such as welding speed, volts and amps, which serves as verification and documentation of the whole weld.
- The system will also monitor material temperature during welding. If this goes above the approved interpass temperature, welding will stop and only resume when the temperature drops to the accepted level.
The WeldLogic, software, can be used on structures such as plates, pipe welding, plate joining and longitudinal joints on cans and further development is ongoing to improve its capability and allow welding of complicated node connections using this laser scanning method.
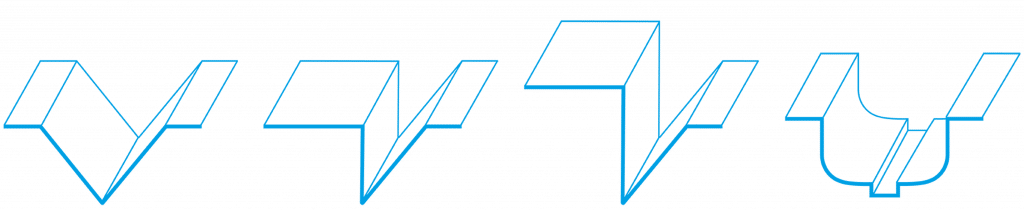
The robot is able to automatically change nozzles to enable the welding torch to reach the root area at the tightest spot of the preparation and to select the best nozzle to match the preparation angles and the configuration as the weld develops out from the root to the final capping runs.
The flexible and compact robot solution developed by Inrotech is intended to break with existing stereotypes, both mechanically, functionally, and logistically. Using their understanding of all aspects of welding, Inrotech have sought to develop automated welding robots that combines high technology and simplicity in a way that moves robotic technology from experts to ordinary people.
LEARN MORE ABOUT WELDLOGIC TECHNOLOGY
Learn how mobile welding robots can solve manufacturing challenges in your industry with WeldLogic Technology.Â
Our industry eBooks dive into specific challenges faced by a variety of industries such as shipbuilding, renewables and many others.