Visit to Odense Steel Shipyard
In 2009, Oshima Shipyard did not have any welding robots in their assembly lines, and the shipyards understanding of robotics for productivity enhancement was limited. The idea of incorporating robots into its production, similar to the offline systems used by larger shipyards at the time, seemed unattainable.
However, during a visit to Odense Steel Shipyard in autumn 2009, Oshima Shipyard encountered a unique mobile welding robot in the production line that caught their attention.
“Unlike the large gantry robots and offline systems they observed, this robot required minimal setup by operators. They simply input a few commands for the robot to follow, directing it on which direction to weld and how many jobs to complete. Remarkably, the operator did not need input data from CAD drawings or engage in any programming. Once set up, the operator could move on to other tasks while the robot autonomously carried out its welding assignments, even allowing for breaks. This demonstration left a profound impression on us.” says Mr. Masahiro Shiraki, Project Manager, Oshima Shipyard, Japan.
Subsequent visits to Odense Steel Shipyard provided them with insight into the engineer behind this innovative mobile robot: Mr. Flemming Jørgensen, the founder of Inrotech A/S. Through multiple meetings, Mr. Jørgensen shared his ideas for welding robots and proposed unique solutions tailored to their needs. His expertise and ability to turn seemingly impossible challenges into viable solutions were evident, inspiring confidence the shipyards capabilities.
“It became clear from our interactions with Mr. Jørgensen that he possessed a wealth of knowledge and experience, with a determined mindset to overcome obstacles. This commitment to his ideas, even in the face of new challenges, was particularly impressive. Overall, our encounters with Mr. Jørgensen and the innovative mobile robot developed by Inrotech left us convinced of their capabilities and motivated us to explore the possibility of collaborating with them further”. continues Mr. Masahiro Shiraki.
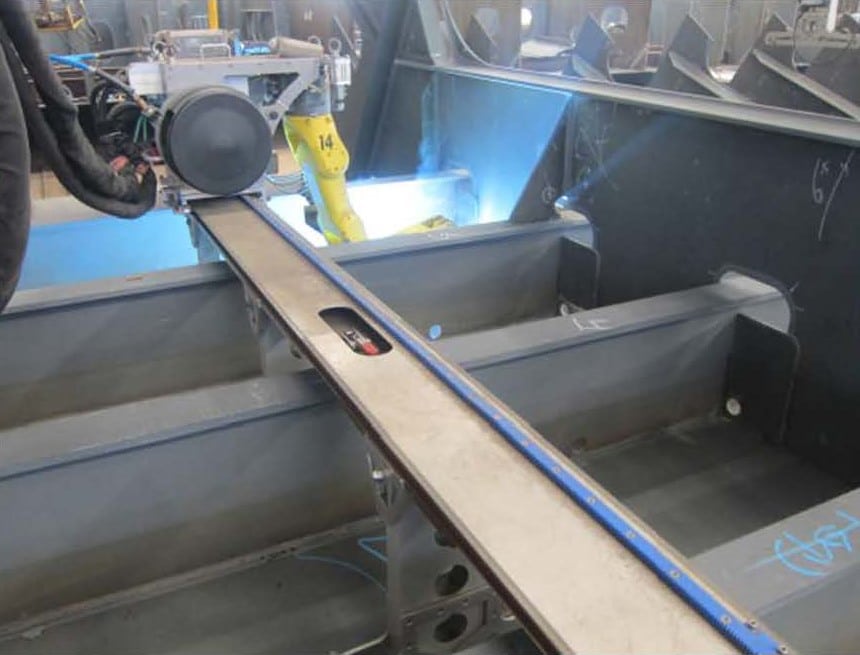
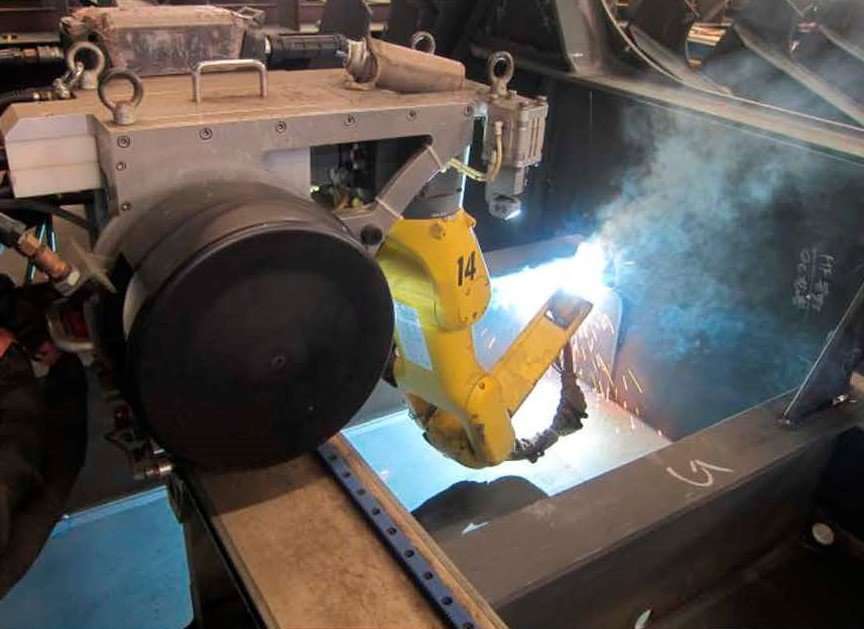
User-friendly welding technology
Ultimately, Oshima Shipyard made the decision to engage Mr. Flemming Jørgensen to develop the inaugural welding robot for their sub-assembly line.
“The technology embedded within Inrotech’s robots is both advanced and user-friendly. These robots boast a lightweight design, making them easy for operators to set up on blocks, and possess the capability to weld any job required within our production line. We have encountered minimal issues with this technology, demonstrating its adaptability to various welding tasks. continues Mr. Masahiro Shiraki.
Over the course of 13 years utilizing Inrotech’s mobile robots, Oshima Shipyard have witnessed significant productivity enhancements and consistent high welding quality. This success has prompted them to reassess its objectives and raise the standards of what can be achieved with the integration of Inrotech’s welding robots.
“As we continue to introduce new products into our production line, we anticipate encountering new challenges. However, we are confident in Inrotech’s ability to address these obstacles. Over the past 13 years, Inrotech has proven to be receptive to our feedback, continuously offering innovative solutions. Moving forward, we envision Inrotech remaining our trusted partner in production, ensuring high welding quality. Currently, we have invested in additional robot solutions from Inrotech to further enhance our operations”, says Mr. Masahiro Shiraki.
In 2023 Oshima Shipyard invested for third time in 5 welding solutions giving them a total of 18 Inrotech-Classic welding robots deployed. These have been used in building bulk carriers for many shipping companies in and outside of Japan. To date, they have built bulk carriers from twenty five countries including Japan, about 53% from Japan and about 47% from outside Japan.