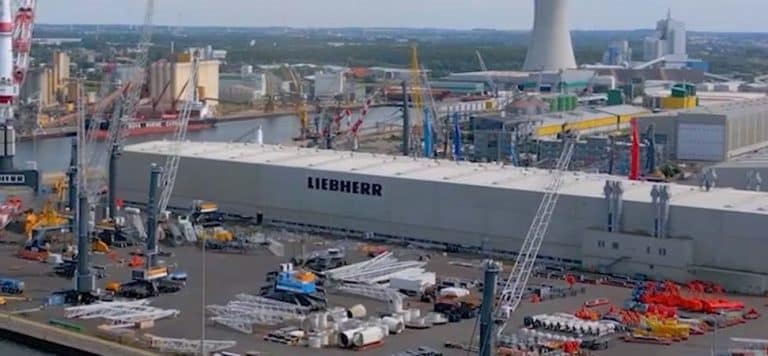
Crane manufacturer Liebherr Rostock Streamlines Heavy-Duty Welding with the Inrotech-Crawlerâ„¢
WELDING AUTOMATION TURNS COMPLEXITY INTO CONTROLLED EFFICIENCY Liebherr Rostock, one of the leading European manufacturer of maritime handling technology, continuously seeks innovation in production processes